Covering the entire production process with one technology
Dispensing small and smallest quantities with volumetric precision and speed often presents major challenges for companies in the medical technology, automotive, electronics, biochemistry, and photonics industries. It is not uncommon for industrial manufacturing companies to integrate various dispensing systems from different suppliers into their lines in order to meet the chemical and physical properties of all materials to be mixed and dispensed. The preeflow brand, whose dispensing technologies can process silicones, adhesives, greases, oils, resins, sealants, or pastes and much more in the currently widest possible spectrum, works reliably and accurately even at extremely high cycle rates.
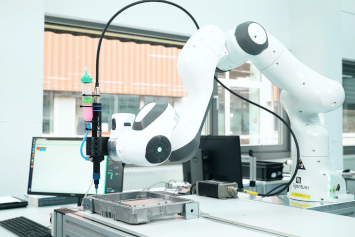
preeflow ECO-PEN and ECO-DUO SERIES can be easily integrated into existing production processes
One-component dispensing systems (eco-PEN), spray dispensers (eco-SPRAY) and two-component variants (eco-DUO) are available and based on the operating principle of progressive cavity pumps. They are equally suitable for manual operation and fully automated use. The so-called endless piston principle ensures pulsation-free and purely volumetric dispensing and delivers material of varying viscosity, unchanged throughout the entire process.
The above-mentioned designs are continuously adapted by an internal research and development team to an increasingly wide range of industrially processable materials, considering parameters such as material composition and its viscosity. The dispensing of adhesives – light-curing, thermosetting, anaerobic, shear-sensitive – is just as simple as the application of solder pastes, the application of thermal pastes or the dispensing of LED resins, to name but a few. The programmable suck-back effect guarantees a clean, controlled thread break with any material, without dripping.
One solution for each dispensing task
Constructively, and in view of the to control technology, different systems are designed specifically for different industrial tasks.
Like the other two dispensing systems, the spray dispenser is based on a rotating, completely pressure-tight, displacement system. Defined rotary movements of the rotor displace the material volumetrically in the stator and convey it into a processor-controlled low-flow spray chamber, where precise atomization and spraying takes place. The spray dispenser can be used in manual or automated mode, using low to high viscosity material to create a well-defined edge and with minimal overspray, which can be atomized either continuously or sporadically.
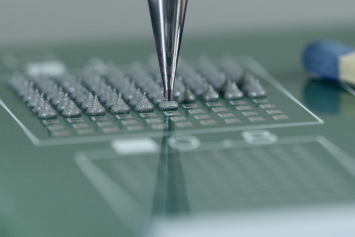
The precise dispensers are perfectly suited for dosing very small quantities of abrasive materials
The one-component dispenser was designed for single-component fluid dispensing. Precise dispensing of aqueous to pasty liquids is possible with even the smallest quantities. The technical design allows the one-component dispenser to be used independently of viscosity fluctuations and ensures clean dispensing – in manual operation, as a desktop device, or automated via a control unit.
With two-component dispensers, systems for the traditional processing of various two-component materials can be selected, or a model that is technically adapted to the requirements of materials which are extremely difficult to mix. The classic two-component dispenser is available in three designs, determined by the quantity to be dispensed. Application is either via static mixing elements, in which the two components are mixed before application. Or – perfect for all viscous two-component materials that are difficult to mix – via a mixing capsule with optimized dead space.
Streamlined warehousing and reduced service costs
The technologies mentioned above can be used as stand-alone units or according to the requirements in a production line throughout the entire process. All systems have the same control system with integrated pressure monitoring and enable the setting of dispensing quantities, mixing ratio and even dispense time. Each control unit is calibrated, and the various functions parameterized via a standardized terminal program. An integrated motor monitoring system serves as an overload protection for the dispensers and can process error messages and pass them on to a higher-level system if required.
If manufacturers use the different dispensers at different stages in a process, such as traditional bonding and the subsequent spray sealing of the fully assembled board, they benefit from the same active principle at both process steps and invest in process reliability through homogeneous structures. Finally, the use of systems from one brand can significantly simplify the storage of consumables and spare parts. The planning of service calls becomes much easier when using the same technology and ultimately results in a reduction in maintenance costs.
The video below shows an application example:
You are currently viewing a placeholder content from YouTube. To access the actual content, click the button below. Please note that doing so will share data with third-party providers. |
---|