Customer requirements demonstrably exceeded by a factor of four
Introduction
Service and maintenance costs are key to reducing the total cost of ownership of production machinery – and not just in high-performance processes. Against this background, the US subsidiary of a well-known German automotive supplier recently inquired with preeflow. The company uses an extreme pressure lubricant to protect components against corrosion and seizing. Each lubrication process provides 100 mg of lubricant directly from a dispenser and with the aid of piston pumps. The actual dispensing process takes 1.4 seconds. The next 100 mg of lubricant is then dispensed after a 4-second pause. This results in a daily runtime of approximately 21.75 hours on weekdays and 11 hours each on Saturdays and Sundays, with their shortened operating periods.
The issue: maintenance costs too high
The 40 bar operating pressure needs to be adjusted down prior to dispensing, and this has been identified as a neuralgic point in the process. Agglomeration occurs at this point due to the separation of oil and particles. As a result, the lubricant – which is already extremely abrasive due to its high particle density – poses a high risk of causing wear, as well as causing the dispensers to clog.
These two factors necessitate the complete replacement of all valves every 4 weeks, at a cost of around $1,000 per valve. Extrapolated to 30 parallel-running lines, that's $360,000 per fiscal year. The company set out to reduce that excessive cost and saw the potential to do so by technically modifying the dispensing system.
From the field into the lab: Test layout and technical settings
The preeflow team led by Tobias Unger was commissioned to run a series of tests to evaluate whether approximately 228,000 to 230,000 dispensing cycles could be executed over a period of 30 days. The key constraint was that quantity variations of only min/max 50 mg were permitted.
It was further agreed that specific statements and image evidence would be provided regarding the effects of the abrasive lubricant on the preeflow components.
The tests were performed with three eco-PEN600 with DC-coated rotors + VisLas and using two eco-Control EC200 2.0. The software was upgraded to be able to record and export motor data. A flowplus-MONITOR QC was also deployed.
No data was available on the viscosity of the Regular Grade Anti-Seize & Lubricating Compound product under test. Details of the oil used and the graphite, copper flake, aluminum powder and zinc oxide fillers were provided prior to testing.
Testing was performed on a test rig arranged in a T-shape. The test material was first transferred to different containers, as the ones it had been delivered in were deformed. The dispensers, in their T-shape layout, were connected to control units on the left and right according to their arrangement and ran in 2N (synchronization) mode. The middle dispenser was connected to a control unit, which was operated in single dispenser (1N) mode. All three dispensers were centrally connected to the MT-XS. The system was calibrated to an assumed density of 1.24 g/cm³.
The average output of the first 10 dispensing shots after calibration was 0.100 g each in the left and middle dispensers, and 0.099 g in the right dispenser. The lubricant was dispensed by quantity, and at a defined rate of 3.750 g/min, corresponding to a dispensing time of 1.6 seconds. The pause between shots was 0.4 seconds.
Test results promising
After 230,000 shots, despite the abrasive properties of the test substance, the internal diameters of the dispensers hardly changed measurably, as shown in Figure 1. The left dispenser now takes 0.107 g of material instead of 0.100 g; the middle dispenser 0.103 g instead of 0.100 g; and the right dispenser 0.108 g instead of 0.099 g initially. From these minor differences it can be deduced that the abrasive medium has only an insignificant influence on the material quality, even with a very large number of single shots.
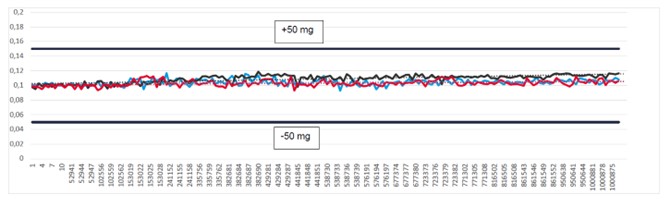
Fig. 1: In 1 million dispensing shots consistent quantities within the required +/- 50 mg. (Source: preeflow)
The test was continued for research purposes after reaching the customer's target (230,000 dispensing shots). The preeflow team hoped that this would provide concrete data on the duration of the test series through to total system failure. When does leakage occur? When does the dispensing pressure drop? Questions like these remained unanswered, even after 1,000,0000 dispensing shots, as no significant changes were measurable (Figure 2). Even the visible wear caused by the abrasive high-pressure lubricant remained within limits (left now 0.106; middle 0.114; right 0.106). The final visual inspection also showed that all rotors were in excellent condition. The stators exhibited merely the expected wear, which in any case did not deviate significantly from the original, at an average of 3% (outer diameter) and 8%, respectively.
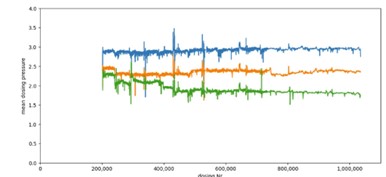
Fig. 2: Stable dispensing pressures from the first to the millionth shot. (Source: preeflow)
Conclusion
These values prove that the 230,000 metering shots required by the customer can be surpassed many times over, and even then, no signs of failure are measurable under laboratory conditions.
Switching from piston pumps to the eco-PEN600 thus guarantees the customer demonstrable savings, as the long dispensing time means it is no longer necessary to replace valves every 4 weeks. Moreover, eco-PEN600 maintenance costs are reduced still further, even in long-term use, as it has been proven that the DC-coated rotors are non-wearing, and the variations in dispensing quantity in a single shot are negligible in view of their low value (max. plus → 18.9 mg / max. minus → 7.3 mg). All the equipment – starting with the dispenser – exhibited zero leakage. No substances containing oil could be detected either there or on pipelines and fittings. Nor were there any detectable quality defects due to viscosity differences. It can be assumed that recalibration can increase the achieved 1,000,000 dispensing shots at comparable quality, and with no material fatigue.