Bonding of catheter components
The use of catheters covers almost all medical specialties. Whether in intensive care medicine for ventilation, in urology as a bladder catheter or in cardiology as a heart catheter – to name just a few examples. Depending on their design, they are used for a wide variety of tasks.
Basically, the manufacture of a catheter always begins with the extrusion of the tubes, which in the next step are bonded to the so-called connectors. This adhesive connection must simultaneously ensure the tightness of the catheter. An optimal process combines extrusion, cutting and bonding via an automated process, since the potential for error is highest during manual joining. This development suggests that the work processes in the corresponding companies will also be further automated.
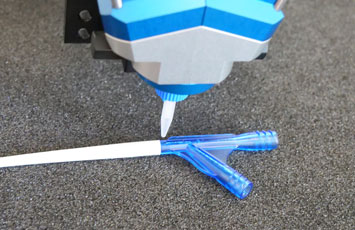
Catheters: Bonding in catheter manufacture with preeflow
But especially the bonding of the individual catheter components is still often done by hand. Thereby precision and cleanliness plays a crucial role in the manufacture of medical devices. At this point we provide an optimal solution with our precise 1- and 2-component micro dispensers.
By the endless piston principle, on which all our dispensers are based, a continuously volumetric dosing is possible. Thus the process is gentle and with low shear force on any media independently of viscosity. The direction of flow can be reversed, this leads to a clean cut-off string and dripping of the medium is prevented.
Our micro dispensers operate in the micrometer range with an absolute accuracy of +/-99 %. This means that the smallest amounts of adhesive can be applied to the tubes, always with constant volume. This quantity can be adjusted so that after attaching the balloons, sleeves, connectors, etc. enough material is available to firmly adhere the pieces together, but so little that no excess material is squeezed out. A more precise dosing in an environment that demands absolute cleanliness and sterility is not possible.
Another benefit is the ease with which our products can be integrated: The microdispensers are designed to be used in any manufacturing process – from simple manual workstations to fully automated production lines. The required hardware is assembled as needed. The user only has to connect it to the existing machines, calibrate it once and the dosing pump is ready for use.
It is possible to start signals for dosing directly via the associated controller, via a foot switch or via a master control unit to. Unlike piston pressure sprayer, the use of this equipment means that the hands of the workers are free for bonding the catheter. So the job is done faster and cleaner, and more catheters can be manufactured in the same time.
Easy and fast cleaning of the dispenser
In addition to the already mentioned advantages of our micro dispensers compared to conventional piston pressure syringes, we would like to point out the cleaning of our preeflow dispensers. This is very simple and quick. For thorough cleaning, the dispenser is disassembled and the individual parts are cleaned with detergent and brushes. It is then reassembled and ready for immediate use. We describe this process for you in a virtual operating manual on Youtube.
- The pressure sensor fluid sensor flowplus 16 from ViscoTec guarantees optimal safety of processes when transporting media.
- preeflow Dispenser for dispensing smallest amounts of fluids and pastes.
- The dispenser and control unit are perfectly matched to each other.
Equipped in this way, nothing more stands in the way of automated gluing in catheter production. With the same personnel, a larger number of catheters can be manufactured in this way to continue to meet the increasing demand. At the same time, material consumption is optimized and rework is eliminated, which contributes significantly to cost reduction. We guarantee absolute repeatability and process reliability for your process.