Mastering the challenges of heat management
Thermal interface materials (TIM) are applied whenever heat has to be dissipated from a component. For example, they are used to fill gaps between two components - from the smallest components in electronics manufacturing to the production of electric vehicles. In addition to heat dissipation, some of the pastes also offer protection against mechanical influences or vibration.
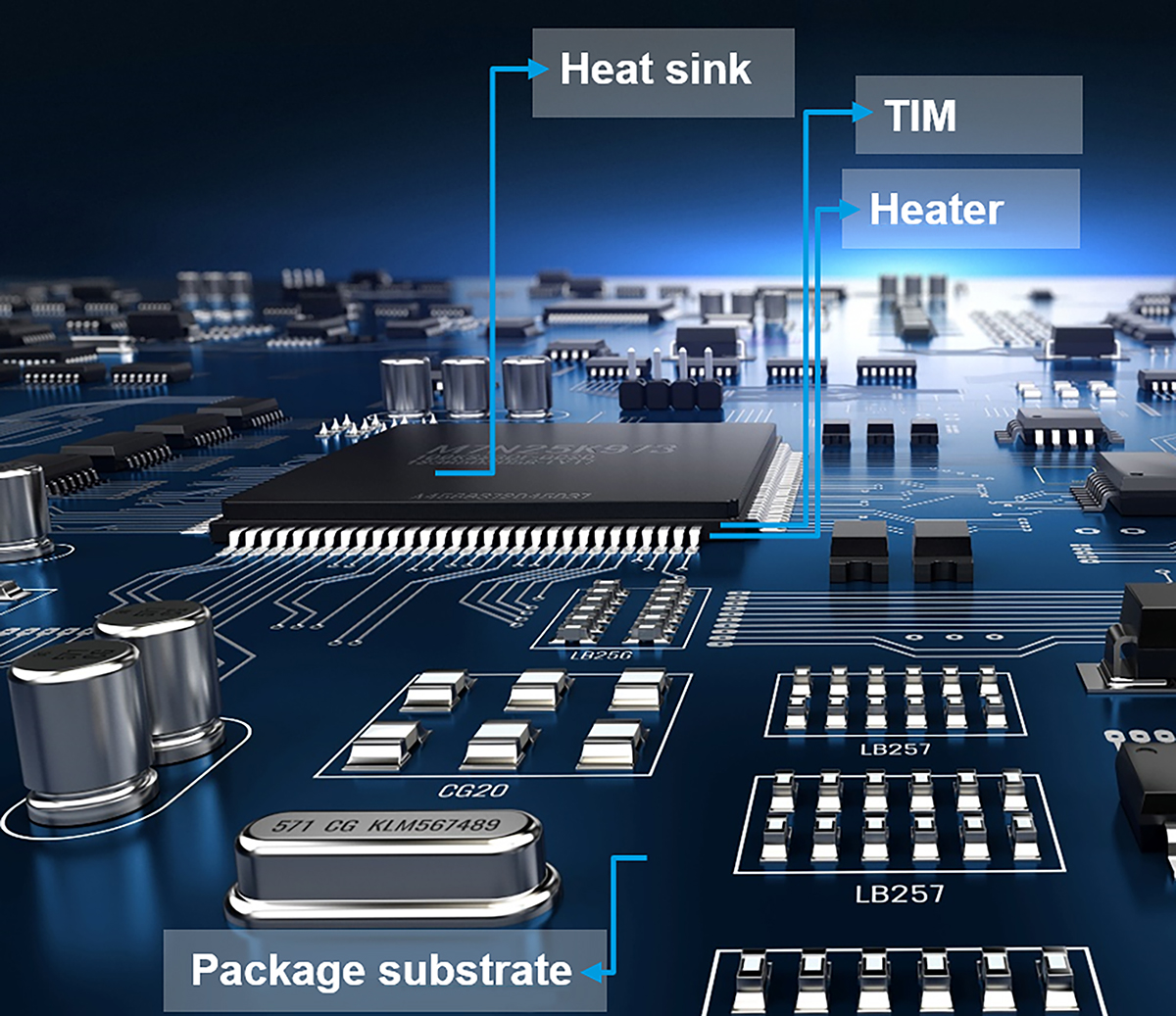
The structure of a printed circuit board
Challenges in the dispensing of thermal conductive pastes
When working with a highly viscous, abrasive paste application, the goal is: Achieve a stable, repeatable process with a long service life of the dispensing system. The biggest challenges here are:
- Avoiding air gaps: Air is a comparatively poorly conducting material. Therefore, cavities between small components in electronics manufacturing must be bonded without air, and gaps must be filled. preeflow enables the application of fluids and pastes without trapping any air.
- Processing highly viscous materials: The solution: To keep the dispensing pressure as low as possible - with regard to sedimentation too. This means achieving a process speed of 20 to 40 % of the maximum possible volume rate with the largest possible dispenser size.
- Dispensing materials with abrasive fillers
(constitution, distribution, sedimentation): Fillers differ in their nature and form, and distribute differently in the carrier material. This makes them a particularly critical and unpredictable factor in the dispensing process. Due to the properties of the ViscoTec continuous piston principle and suitable dispensing components, preeflow microdispensers are ideally suited for handling highly filled materials.
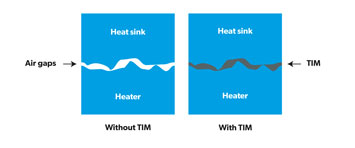
Comparison with and without thermal paste
The right dispensing components for thermal pastes
Depending on the dispensing quantity, different components must be selected. The following are available for selection: Diamond Coated (DC) rotors and VisLas stators. The DC rotors are produced in a combination of different coating and finishing processes specially developed for this purpose. This unique multilayer principle makes it possible to achieve a previously unattainable surface hardness for rotors made of metal. This significantly exceeds the surface hardness of standard rotors and also offers advantages in terms of friction between rotor and stator. The counterpart to the DC rotor is the already established VisLas stator, which is particularly suitable for abrasive materials.
preeflow offers flexible dispensing systems for a wide range of applications. Due to a modular design of the dispensers, individual components can be replaced at any time and adapted to the current dispensing process and all its requirements. With the right components, the service life of your dispensing systems is extended. By saving time, nerves, and money. Make the right choice!
To the ViscoTec Whitepaper "Heat management"
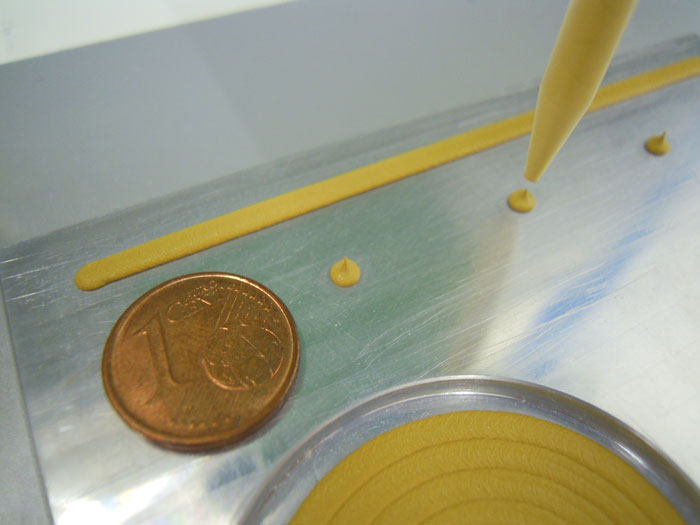
Dispensing of abrasive thermal paste...
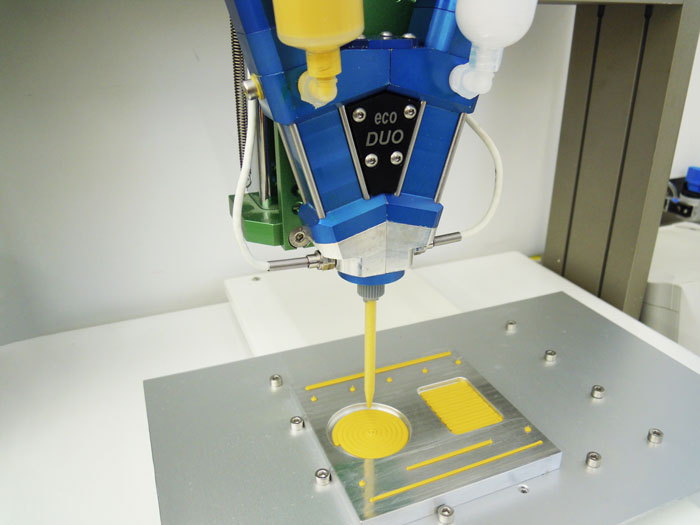
...with the preeflow eco-DUO dispenser