How to ensure reproducible quality in end products
One of the most important parameters in a dispensing process is the resulting dispensing pressure. The optimal conditions for a functioning and process-safe setup can only be achieved by controlling this pressure.
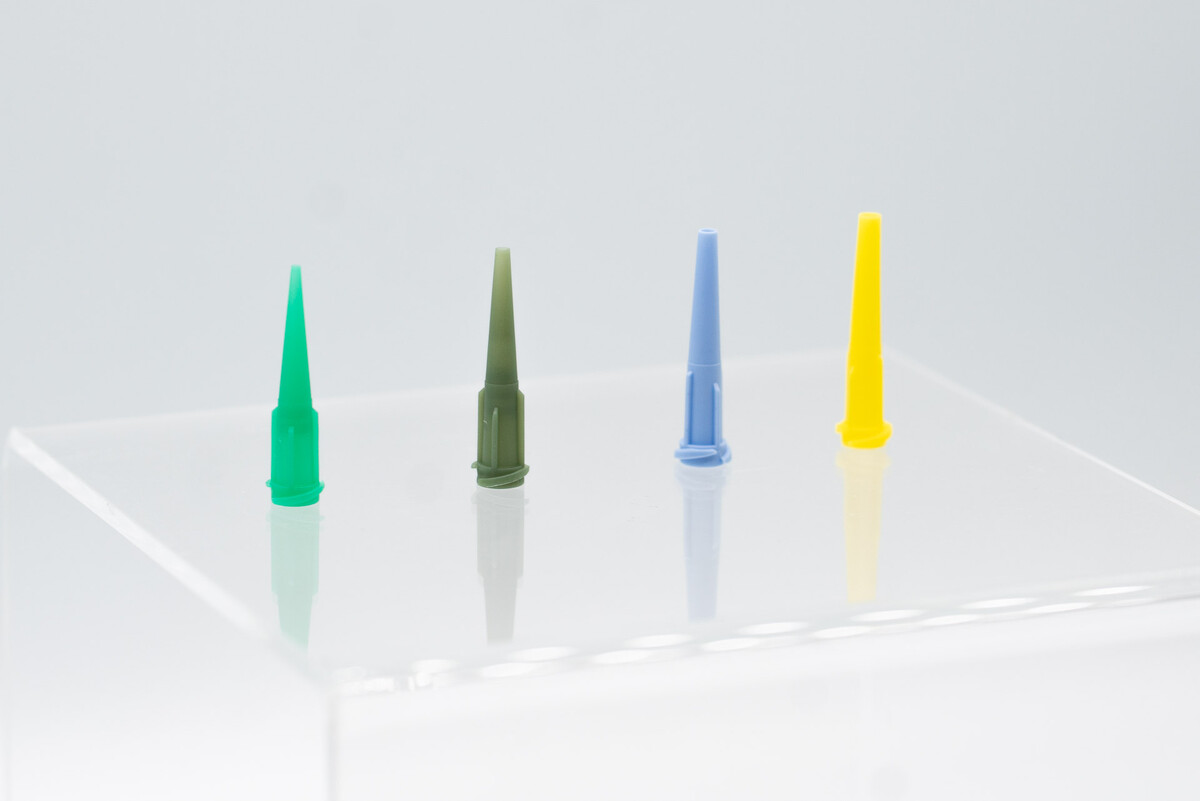
Overview of preeflow consumables dispensing needles
The best example where the dispensing pressure becomes a critical parameter: The application of partly highly viscous and filled material in combination with high flow rates. If suboptimal dispensing tips are used here - i.e., with an inner diameter that is too small - the pressure increases. The result is that the material is partially squeezed. This often results in less than precise dispensing results with a lack of repeat accuracy. The quality of the end product can no longer be 100% predictable.
With this information, it is therefore advisable to make the selection of the correct dispensing needle - suitable for the process and the material - an integral part of the evaluation, and only then start dispensing.
The following factors should be considered in the decision-making process when selecting a dispensing needle: Needle material, internal geometry, and needle length. These needle parameters influence the dispensing result and therefore the quality of the end product. Furthermore, these three factors extend the range of possible process parameters and therefore enable further individualization of a dispensing process by the customer.
Users can define the dispensing conditions of their application process even more accurately, due to the expansion of the portfolio with 2 new conical dispensing tips, in sky blue (inner Ø 2 mm) and in yellow (inner Ø 2.5 mm). The enlarged inner and outlet diameters ensure a stable dispensing setup and therefore an optimally balanced interaction of dispensing speed and volume flow.
The following test series illustrates these relationships on an eco-PEN600. The A component of a widely used gap filler was used as the test material. Throughout the course of the test, the flow rate was adjusted in combination with different dispensing needles.
The following pressures were detected:
|
3,2 ml/min (20 %) |
6,4 ml/min (40 %) |
green (ID 0.84 mm) |
9 bar |
15 bar |
olive (ID 1.6 mm) |
4 bar |
7 bar |
light blue (ID 2.0 mm) |
3 bar |
5 bar |
yellow (ID 2.5 mm) |
3 bar |
5 bar |
open end (without needle) |
2 bar |
3 bar |
The lower pressure when using the light blue and yellow dispensing tips is clearly visible in the series of collected data. The process conditions improved in this way provide the basics for being able to achieve higher dispensing speeds and volume flows, while at the same time guaranteeing the same repeatable quality. Both needle options use the established Luer-Lock connection and can therefore be used for all preeflow products of the eco-PEN family.
The yellow and light blue options are already available.