Les limites techniques : comment les surmonter lors du dosage et du collage
D'après des statistiques, la part des automobiles connectées sera d'environ 97 % en 2035 ; la situation devrait être similaire en Europe. Ces dernières années, on a déjà pu constater une augmentation du degré d'automatisation sur l'ensemble de la chaîne de création de valeur dans la construction automobile, à commencer par les OEM et les fournisseurs de systèmes et de composants, jusqu'aux fabricants d'outils et de moules. À chaque fois que cela était et est possible, les opérations manuelles sont automatisées en totalité ou en partie. Les fabricants de haut-parleurs encastrables haut de gamme ont décelé le potentiel de l'automatisation et suivent le mouvement. Mais les défis à relever sont nombreux.
Si les fabricants de systèmes audio destinés à l'industrie automobile veulent rester les interlocuteurs privilégiés en tant que partenaires de l'industrie automobile, il leur faut non seulement améliorer les performances au niveau de l'assemblage, mais également garantir la qualité. Une difficulté est que les composants des haut-parleurs sont en grande partie collés entre eux. Seule une technologie capable de garantir des cadences élevées et un dosage précis des colles est donc à même de permettre un bon passage de la fabrication manuelle à la fabrication semi-automatique ou automatique de haut-parleurs. En règle générale, les principaux composants d'un haut-parleur, à savoir la bobine, l'aimant permanent et la membrane, de même que les pièces intermédiaires, sont toujours montés dans le même ordre : d'abord le joint d'étanchéité qui entoure le haut-parleur, puis la connexion de la bobine, la jonction du cône au cache noyau et à la bobine, et celle du cône à la couronne en mousse et au châssis. La couronne dentée est ensuite reliée au boîtier, le cône à la bobine, puis la bobine au spider. Une fois que la plaque supérieure a été fixée au châssis, l'aimant et la plaque sont reliés entre eux. Selon le pays de production, ces opérations sont réalisées manuellement ou seulement partiellement automatisées.
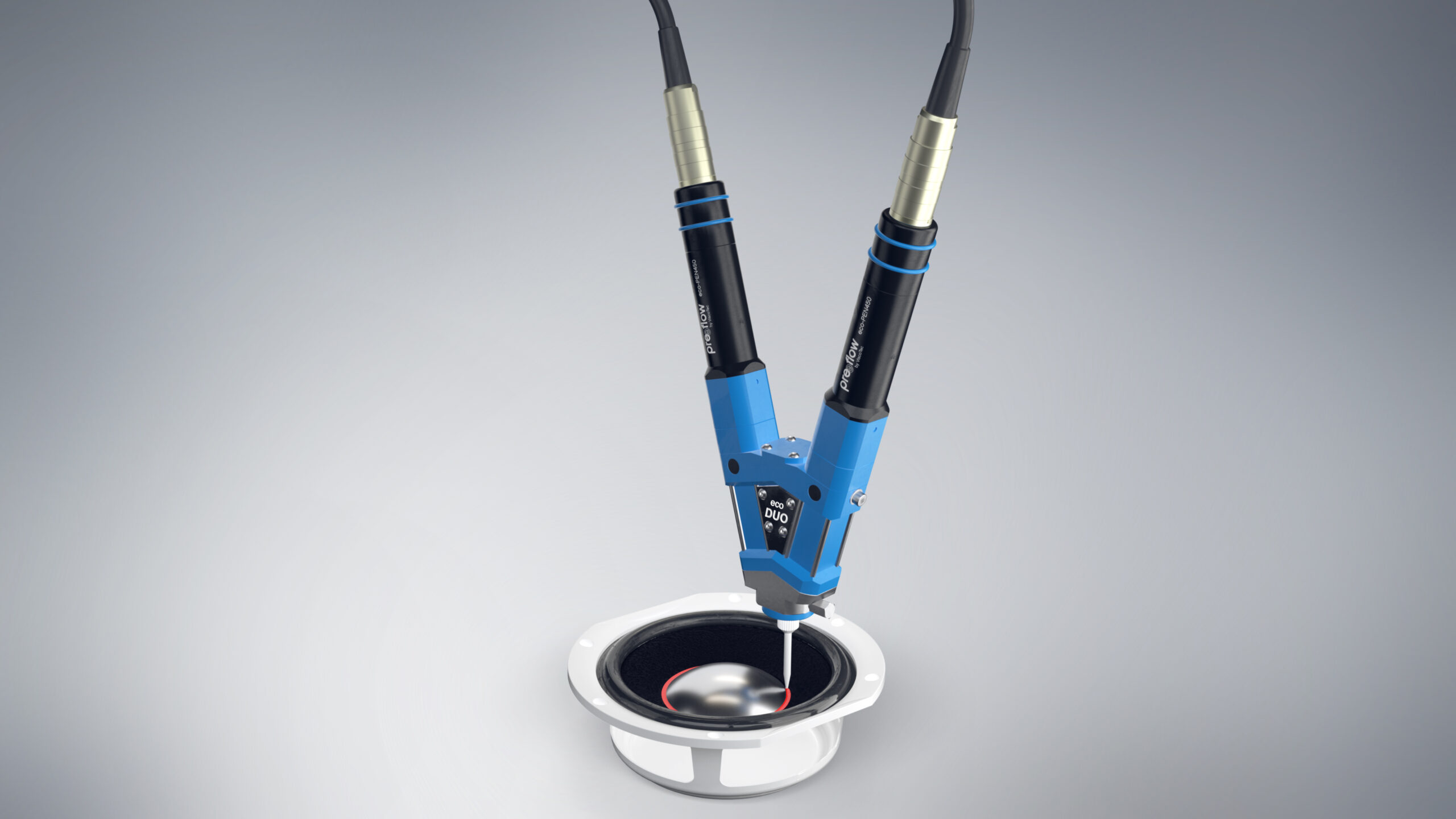
Application de colle 2K dans la production de haut-parleurs
Composants et colle : l'accord doit être parfait
Un paramètre important : la colle. Elle doit être parfaitement adaptée aux matériaux employés. L'acier au carbone, la ferrite frittée, le néodyme, le caoutchouc et les mousses sont par exemple collés à l'aide de résine époxy (monocomposant ou bicomposant) ou acrylique. Grâce à cet assemblage, les oscillations électriques sont transformées avec précision en vibrations mécaniques. Une surface vibre alors en rythme et émet le son.
Par conséquent, tout défaut d'assemblage de forme ou de matière au sein du système que constitue le haut-parleur entraîne des pertes de qualité audibles. Très importante : la suspension de la membrane. C'est elle qui permet à la membrane de bouger et qui la relie hermétiquement au saladier. Il est intéressant de noter à cet égard que par leur principe, les petits haut-parleurs diffèrent à peine des casques. La seule différence est que la membrane de ces derniers est placée directement sur l'oreille. La membrane d'un casque est normalement capable de restituer toutes les fréquences audibles de 20 Hz à 20 kHz. Alors que lors d'une écoute naturelle, les fréquences inférieures à 150 Hz sont ressenties par le corps tout entier et non pas seulement captées par les oreilles, ce n'est pas le cas avec des casques. Vu que les principes physiques des haut-parleurs et des casques sont pratiquement les mêmes, la fabrication des deux produits peut théoriquement être automatisée si un dosage précis peut être assuré à grande et à petite échelle même à des cadences élevées.
Un faible coût total de possession grâce à l'absence d'entretien
preeflow est une technologie qui maîtrise avec brio cette précision et ces cadences et qui, de surcroît, fonctionne de façon vérifiable sans entretien depuis trois ans dans l'installation d'un fabricant de haut-parleurs. Le seul fait que le système de dosage ne nécessite aucun arrêt de l'installation est un indicateur du haut niveau de performances possible dans la fabrication, et a en même temps un effet extrêmement positif sur le coût total de possession. Toutes les possibilités s'ouvrent aux entreprises désireuses d'automatiser de telles opérations de dosage et de collage, car preeflow s'adapte à pratiquement toutes les tailles et formes de haut-parleurs. Quels que soient les contours souhaités ou nécessaires et les vitesses de dosage : la flexibilité des fabricants de haut-parleurs quant au développement de leur gamme est assurée. Les zones critiques comme les courbes sont parfaitement maîtrisées grâce au ralentissement du cordon de dosage, ce qui prévient les accumulations de matière aussi sûrement que le chevauchement inesthétique des extrémités des cordons. Concernant les coûts, preeflow est une technologie efficiente, avec laquelle le produit ne goutte et ne file pas, ce qui représente un plus tant du point de vue des coûts que de la durabilité.
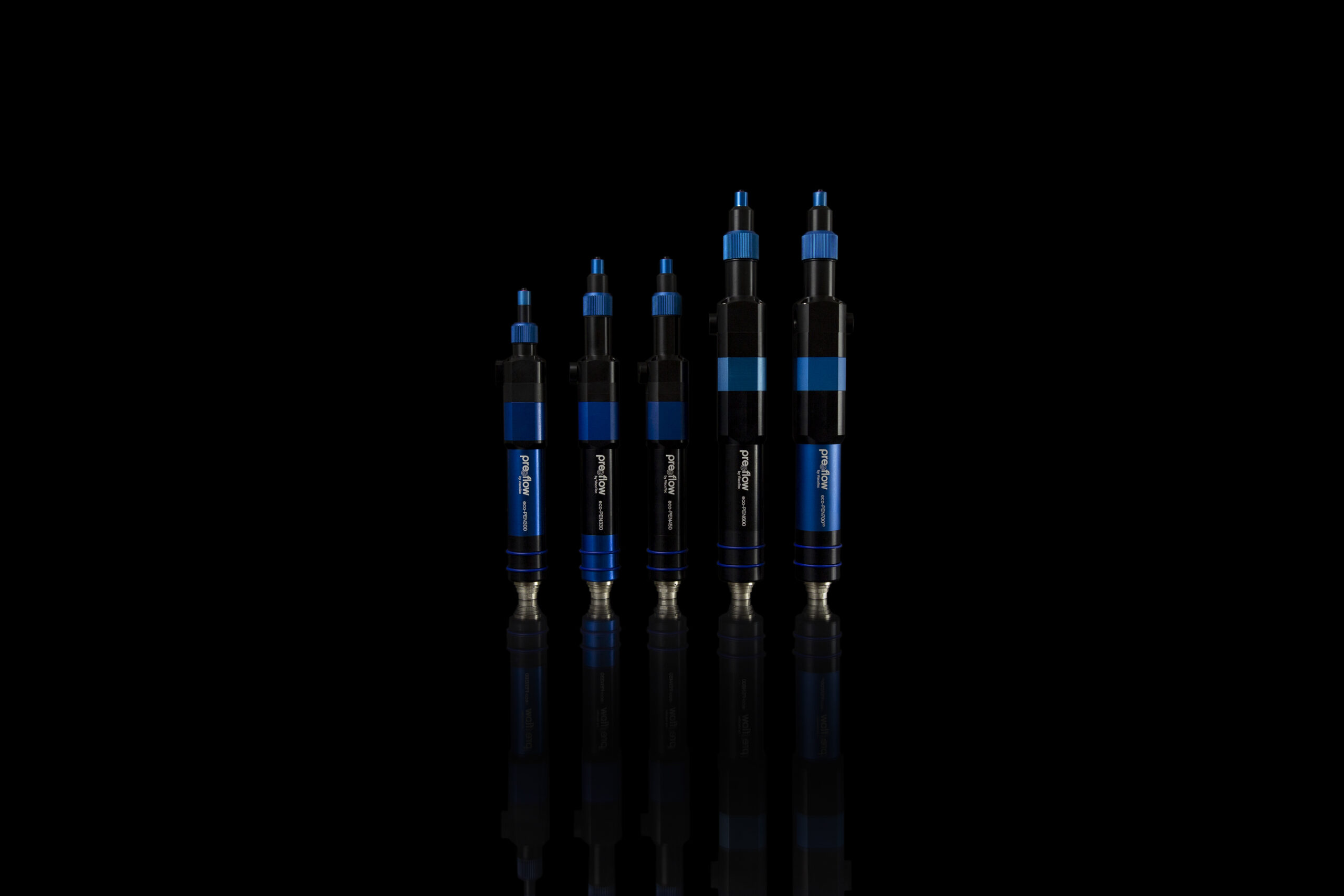
La série de doseurs monocomposants preeflow eco-PEN
Intégration dans des processus nouveaux ou existants : sans faille
Les fabricants de haut-parleurs utilisent au choix des doseurs volumétriques de précision du type eco-PEN et eco-DUO. Tous deux assurent un dosage stable même à des cadences élevées. Le type de collage des haut-parleurs varie d'un fabricant à l'autre, tout comme la constitution précise et les matériaux utilisés par le fabricant de haut-parleurs ou de casques. Vu que preeflow maîtrise et couvre la totalité des procédés existants, son intégration dans un processus n'est pas compliquée. Qu'il s'agisse du collage de la bobine, de l'aimant, de colles amortissantes pour membrane, de la fixation de fils ou de la protection contre les contacts, outre les colles réticulant aux UV, il est possible de doser également des matières bicomposants et tout autre type de colle d'une viscosité liquide à pâteuse. Une reproductibilité supérieure à 99 % est possible même avec de très faibles quantités de colle à partir de 0,001 ml, une condition indispensable à la fabrication hautement performante (semi-)automatisée de haut-parleurs. Le système de dosage s'intègre dans des lignes existantes ou peut être relié à des robots industriels flexibles sans aucune difficulté. Une flexibilité et des performances maximales sont assurées même après le retrofit ou la mise à niveau d'une installation existante, vu que le produit peut être appliqué sous différents angles et dans différentes positions. Avec preeflow, la question des temps d'arrêt liés aux équipes et aux durées de fonctionnement variables de l'installation ne se pose pas, car cette technologie ne nécessite aucune mesure de préparation ou de finition.